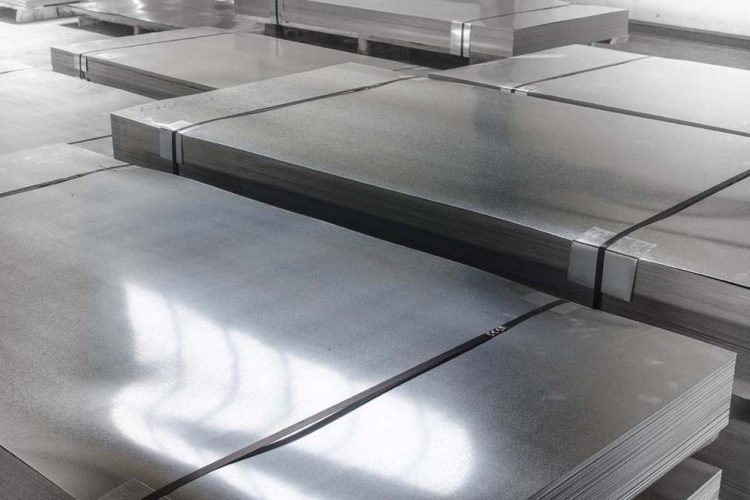
Reducing Metals
There are many large rolling mills, including rolling mills that roll hot steel slabs 16” thick x 160” wide down to steel plate. When we think of reducing, we think of at least 20% thickness reduction per pass or many passes. In all cases, by reducing hot or cold metals, you improve its grain structure. As an example, if you start with a casting or cast slab, and reduce the casting at ambient elevated temperatures, you will improve or change the grain structure. Casting does not always have the best grain structure required for the end product. By reducing a casting, the grain structure is improved or changed. Reducing is sometimes done after the material has been annealed. The softness obtained from annealing is for a substantial reduction. Reducing can also be done to hold an accurate tolerance in thickness. As an example, steel slab up to 6” thick in any width can be reduced 4” in a single pass. This assures a good grain surface.
To do this, it is necessary to have a rolling mill with a large diameter roll. With a small diameter roll, the material will slip and not move through the mill. Roll bite can be calculated with total reduction coefficient of friction between the material being rolled, the roll diameter, and other factors. When the roll bite percentage becomes too large, the roll will not create a roll bite. Roll bite is affected with coefficient of friction. Coolant can also reduce the ability of a large roll bite. Some rolls have a rough surface to assure good roll bite. Again, a large reduction is necessary on the very first pass to improve grain structure. If you only make small reductions, you are only reducing the outer surface. The center of the material does not get reduced therefore, the center or core of the material will have a defective grain structure. This is why large diameter roll 2-high mills are sometimes used for reducing thick material with a high percentage of reduction.
The first pass through the mill makes a high reduction, and the second, third, etc. pass make further reductions. Other passes are usually lighter reductions to hold accurate thicknesses or diameters, especially in the case of rod or wire.
Another purpose of reducing is to increase the hardness of the material, which changes the tensile strength and yield strength of the material. In some cases, customers want full hard material because they want the material to be strong with a minimum amount of weight. Such is the case with steel studs where the material is reduced down to .017” thick. Full hard may vary in different alloys. As an example, if you reduce AISI 1008 to full hard, you start with a yield strength of 30,000 PSI and finish at 90,000 PSI. If you full hard some carbon or stainless steels, you may start at 50,000 PSI yield strength and go to 300,000 PSI yield strength. Some spring materials are made without heat treating simply by reducing the alloy steel. Some full hard materials can be such that the yield and tensile become the same and the material will break like glass when bending. So whether you start with a cast ingot, slab, or strip to increase the grain structure, a high reduction on the first pass is required.
Aluminum foil is made consistently with an accuracy of .0002” thick. You cannot have a large variation in thickness in aluminum foil. Aluminum foil is rolled on a rolling mill generally up to 60” wide. The accuracy must not only be held in the center, but at the edges as well, in fact, throughout the entire width of the strip. Aluminum foil is rolled at speeds up to 3,000 FPM. Low carbon steels are generally made from .012” to .250” thick. With high production manufacturing with progressive dies and complicated forming operations, the next operation after rolling has to produce a consistent product. Shim stock as used in the final drive of an automobile to adjust for gear clearance, as an example, requires high precision shims of various thicknesses. There are many uses for shim stock made on a rolling mill. Such accuracy can be ± .0001”. There are many uses for stainless steel that are roll formed. The thickness must be held consistent and extremely accurate, and at the same time, have a mirror type finish. Some carbon steels are reduced accurately and are chrome plated as used in household utensils.