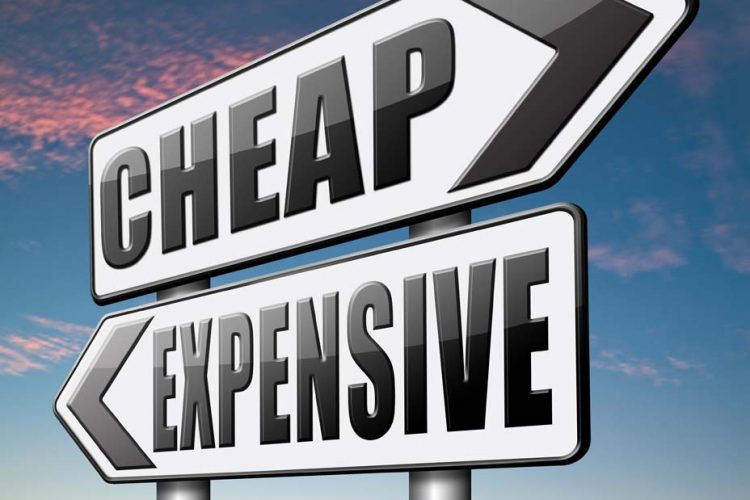
DC Motors and AC to DC Drives
DC motors can do everything AC drives can do, however, the disadvantage of a DC motor is that it requires brushes and these types of motors are open and require some maintenance. Rolling mills usually run around the clock, and DC motors may cause downtime and are expensive to maintain such as the continuous need to be machined, and of course, the brushes wear. However, the amount of maintenance on a DC motor, if maintained properly, can be infinitesimal.
An advantage of an AC to DC drive or rectifier is the cost. Drives can be upgraded utilizing older DC motors. The rectifier system from AC to DC has substantially reduced in cost, and the drive itself is usually less expensive than an AC variable frequency drive. Another advantage of a DC drive is that it can be regeneration. The uncoiler or tension reel can generate a substantial amount of electrical power that can be put back into the machinery so the electrical power generated by the uncoiler tension reel can be utilized at the recoiler tension reel. Another advantage is that DC drives do not require large resistors or sometimes no resistors depending upon the electrical utility. This is because the breaking system on a DC drive can go into the electrical utility for regeneration quickly and bring the drive down to stop quickly without resistors.
Many mills and components still prefer DC variable speed, variable torque drives. These are energy efficient as they only require the amount of energy required to do the work. If a motor has 5,000 HP and only 1,000 HP is needed to do the final pass, it will only use 1,000 HP.
Another benefit of modern electronic DC technology is the fact that you eliminate many relays and expensive conduit and wiring, as controls can be sent from the control console to the motor through small cables instead of a hundreds of wires.
All new variable speed drives can be controlled through Human Machine Interface (HMI) touchscreen controls. Electrical controls and circuits to a rolling mill require experienced rolling mill electrical engineers to design a system based on information obtained from an experienced rolling mill engineer. Of course, speed, tension, thickness, lineal feet, part number, run time, roll replacement/change and any variable involved can be put into a modern HMI touchscreen.