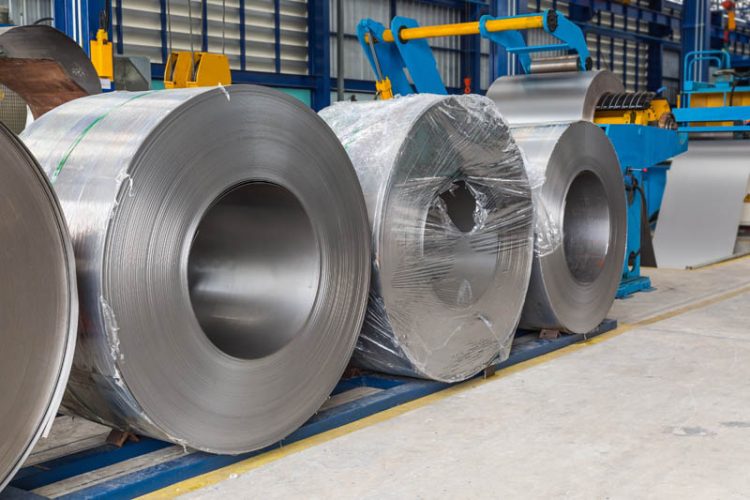
How To Choose A Roll Former
Roll forming is an ongoing bending procedure in which a lengthy strip of sheet steel (normally coiled metal) is passed via rolls mounted on consecutive stands, each set executing only an incremental component of the bend, till the preferred cross-part profile is obtained. Roll forming is perfect for generating continuous-profile components with long lengths and in big quantities.
There are two different types of roll forming machines, Pre-Cut and Post Cut. There are advantages as well as disadvantages to both.
Pre-cut advantages:
- Eliminates expensive cut-off dies and their maintenance
- Buff-free ends
- Simple low-maintenance pre-cut shear
- Ability to hand-feed strips or sheets for low-volume production
- In roofing and wall panel products, pre-cut avoids cut-off distortion because running different gauges and yield with the same roll tooling affects the final shape which may not match the blade even though it is within tolerances
Pre-cut disadvantages:
- Possibility of increased end flare, especially in deeper parts
- Higher strength steels present a larger challenge
- Requires more forming stations making the roll former and tooling more expensive
- Generally requires more floor space
- Shorter parts are more of a challenge and can introduce part quality issues
- Difficult multi-bend parts can be a problem in terms of quality
- Pre-cut may require intermediate guides, especially when running short pieces. Adjusting these guides becomes problematic with multiple width guides
Post-Cut Pros
- Production rate is higher with post-cut
- Better part control in terms of quality
- Reduces end flare considerably-end flare can be controlled
- Better results for high-strength steels such as dual phase and martensitic steels
- Lengths as short as 2-3 inches can be produced
- End straighteners are most effective in post-cut, controlling bow, camber and twist
- No leading edge deformation of the part in post-cut
- Better roll life in post-cut when running heavy gauge and high-strength material because the leading edge in pre-cut hits the rolls with every part
- Friendlier to material deviation in terms of gauge and hardness
- Ability to provide punching/notching during the cut-off operation, possibly eliminating one or more secondary operations
Post-Cut Cons
- Expensive cut-off press and die
- Maintenance costs, especially for the cut-off die
- End burr resulting in rough end
- Distortion on product end
- May require manual feeding of leading end of first part upon introduction of a new coil
- In many cases, all surfaces must be supported in order to avoid end distortion. This is not always possible due to inability to build robust die sections into the die OR the need to leave an opening in a practically close space
The above information is a good guide when deciding how best to address your roll forming needs. Our team of experts are available to help you find the right equipment to fit your specific needs.
With over 60 years of experience and a real focus on customer satisfaction, you can rely on ASP for your next project. We provide a professional renovation and installation services with a real focus on customer satisfaction. We have proven results for setting exceptional standards in cost control, planning, scheduling and project safety. We have experience that gives us a competitive advantage over others in our field.