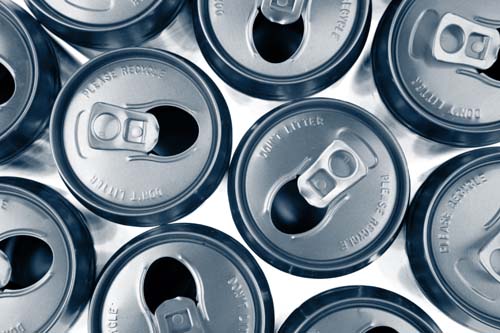
Special Mills and Features
Expanded metal is a common product throughout the world and much expanded metal goes through a rolling mill. These are normally very large 2-high or 4-high rolling mills that are very expensive. The top two rolls is where the reduction is taking place. This mill has only 16” diameter rolls. The lower roll has a sizeable crown with hydraulic cylinders that allows the center rolls to bend substantially when under load. The top and bottom rolls are bending, but the material is a chrome moly alloy steel. The rolls bend safety at no more than 15,000 PSI. The expanded metal goes through the rolling mill flat and level with a slight crown of 1/16” across the width.
Two-high rolling mills with water hydraulic screwdowns are used in aluminum continuous casting lines. The mill can be placed at an angle, which allows the liquid aluminum to be placed in front of the rolling mill. The rolls are generally large in diameter and water cooled to cool the aluminum as it is made into a thick strip. A cast aluminum coil is then placed onto a separate reducing mill to make the light gauges. Aluminum continuous casting lines can be made any width and any thickness. The material is blanked into small diameters and used to make small aluminum cups and containers. Aluminum beer bottles are extruded from cast and reduced in line on an aluminum continuous casting line.
Rolling Mill Rolls
The work rolls in a rolling mill are essential to high quality, consistent rolling. These rolls are engineered and always made by America’s leading roll manufacturer. The alloy forgings and heat treating of the roll is extremely important. As an example, the work rolls can be very hard, up to 65 RC or less, and the back up rolls are always softer say 55 RC to flex under pressure without breakout. They are made from alloy forged steel and are high carbon, high chrome with other elements.