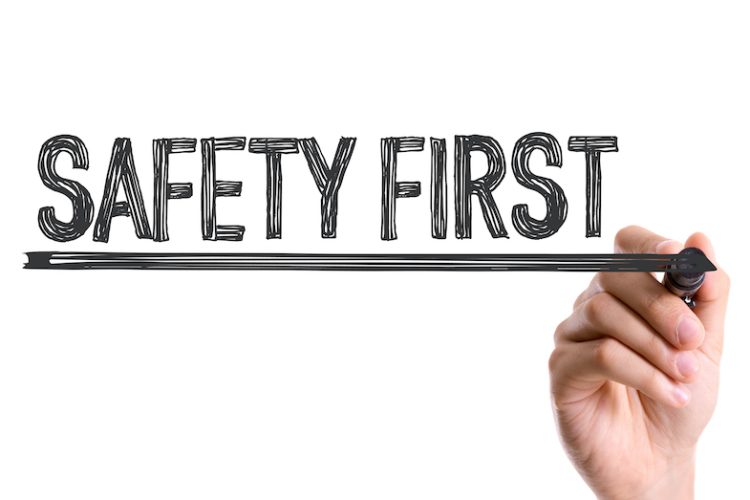
Safety Protocols When Working With Metal Processing Equipment
Metal processing equipment plays a vital role in various industrial sectors, including manufacturing, construction, and infrastructure development. However, operating such equipment involves inherent risks that can lead to serious injuries or even fatalities if proper safety protocols are not followed. Implementing comprehensive safety measures is crucial to ensure the well-being of workers and the efficient operation of metal processing equipment. In this article, we will explore some essential safety protocols that should be followed when working with metal processing equipment.
- Training and Education: Proper training is paramount for anyone operating metal processing equipment. All personnel involved should receive comprehensive training on equipment operation, safety procedures, and emergency protocols. They should be aware of potential hazards and know how to mitigate risks. Regular refresher courses and updates on safety practices are necessary to ensure ongoing competence.
- Personal Protective Equipment (PPE): Workers should wear appropriate PPE to minimize the risk of injury. This includes safety goggles, face shields, gloves, protective clothing, metal-toed boots, and hearing protection. PPE should be inspected regularly, and damaged or worn-out equipment should be replaced promptly.
- Machine Guards: Metal processing equipment often involves moving parts, heavy machinery, and high temperatures. Properly installed and maintained machine guards are essential to prevent accidents. Guards should be in place to protect operators and other workers from coming into contact with hazardous areas, such as rotating blades, sharp edges, or hot surfaces.
- Lockout/Tagout Procedures: Metal processing equipment requires regular maintenance, repair, and cleaning. Lockout/tagout procedures must be implemented to ensure the equipment is properly shut down and de-energized before any servicing or maintenance work is performed. This prevents accidental startup or release of stored energy that could cause severe injuries.
- Adequate Ventilation: Many metal processing operations generate fumes, dust, or gases that can be harmful to workers’ health. Proper ventilation systems should be in place to remove these contaminants from the work area and maintain a safe breathing environment. Regular inspection and maintenance of ventilation systems are necessary to ensure their effectiveness.
- Fire Safety Measures: Metal processing involves high temperatures and flammable materials. Fire prevention measures should be implemented, including the installation of fire suppression systems, fire extinguishers, and smoke detectors. Employees should be trained on fire safety protocols, including evacuation procedures and how to operate firefighting equipment.
- Material Handling and Storage: Proper material handling procedures are essential to prevent injuries and accidents. Heavy metal plates, coils, or bars should be stored and secured appropriately to prevent them from shifting or falling. Workers should be trained in safe lifting techniques and the use of lifting equipment such as cranes, forklifts, or hoists to minimize the risk of strains or crush injuries.
- Regular Equipment Inspection and Maintenance: Routine inspections and maintenance of metal processing equipment are vital to identify any potential hazards or defects. This includes checking electrical connections, lubricating moving parts, and inspecting safety features. Any equipment found to be faulty or in need of repair should be immediately taken out of service until it is properly fixed.
- Emergency Response: Emergency response plans should be in place, clearly communicated to all employees, and regularly practiced through drills. This includes procedures for medical emergencies, fires, chemical spills, or equipment malfunctions. Adequate first aid kits and emergency contact information should be readily available at the worksite.
- Continuous Safety Training and Improvement: Safety protocols should be regularly reviewed, updated, and communicated to all workers. Feedback from employees should be encouraged, and near-miss incidents or accidents should be thoroughly investigated to identify areas for improvement. Continuous safety training and awareness programs help ensure that all personnel remain vigilant and committed to maintaining a safe work environment.
Safety protocols are of utmost importance when working with metal processing equipment. By providing comprehensive training, enforcing the use of personal protective equipment, implementing machine guards, following lockout/tagout procedures, ensuring proper ventilation, and maintaining fire safety measures, among other precautions, the risk of accidents and injuries can be significantly reduced. Regular inspections, emergency response plans, and continuous improvement efforts help create a culture of safety and ensure the well-being of workers in metal processing operations.