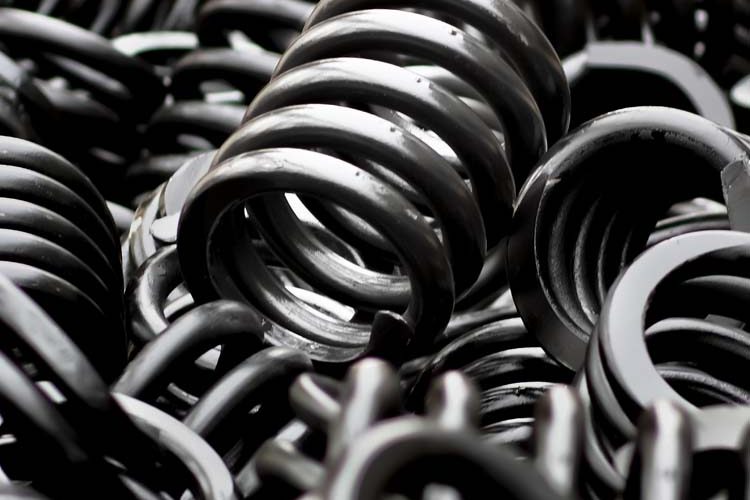
Purposes Of Alloy Carbon Steels
One of the purposes of alloy carbon steel is to improve the quality and physical properties of carbon steel. Many carbon steels have other alloys mixed in such as chrome, molybdenum, vanadium, manganese, silicon, and many other elements. The purpose of alloy carbon steel can be many. However, it is exceedingly difficult to weld high carbon alloy steels because when the weld cools, the carbon steel near the weld becomes very hard, making the steel under the weld unsatisfactory. The only way to weld high carbon steel is to preheat the steel before welding however, this destroys the integrity of the steel. The mill must add columbium or niobium in the steel so that it is strong and welds quickly without becoming brittle. Many ships, tanks, towers, etc. are welded with alloy carbon steels.
Before a product is designed with carbon steels or alloy carbon steels, extensive research is done to not only look at the best consistent quality of available steel, but to look at the cost of each carbon steel product. Seeking the advice of a welding expert to specify, and how the material should be welded, such as ERW, TIG, MIG, etc. All alloy carbons steels become harder (100,000 to 300,000 PSI yield strength) after being rolled or reduced and annealed for further rolling and reducing.
Carbon steels and stainless steels can be made into almost any alloy. An alloy is the mixture of almost any element. The most common high strength, high yield alloy is a chrome moly alloy such as AISI 4140 or 4340. These alloys are commonly used in steel plate and are quenched and tempered. To reduce these steels, cold working or work hardening is a factor to consider because, like stainless and high carbon steels, the material increases substantially in yield strength when reducing.
One of the most useful purposes of alloy steels is in springs or any application where the material has to flex on a continuous basis without breaking. Most steels will crystalize in time even though they are not bent beyond the yield point. As an example, that is why a lot of machinery shafts that take a side load are made from alloy steel. As an example, AISI 4340 is used to prevent fatigue, and the maximum stress the shaft may be under is 16,000 PSI however, the actual yield point of the material is 150,000 PSI. Fatigue and flexing is considered when the material is used in bridge or machinery building. The material, type of construction, welding, machining, etc. must all be considered in the final cost.