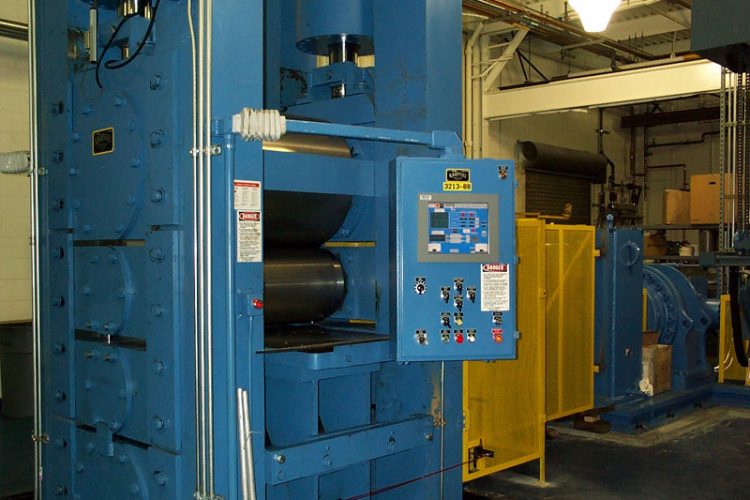
Hydraulic Screwdowns
Practically all new rolling mills today are equipped with hydraulic screwdowns for hot or cold rolling. A disadvantage of mechanical screwdowns is the fact that you cannot adjust accurately while the screwdowns are under pressure. When you want to move upward with a roll gap, you always have some mechanical backlash. Even though you can measure the roll gap, the backlash is still there and the roll gap can drift.
To accomplish this, the operators or machine normally make some adjustment and then come back down again with mechanical screwdowns. Hydraulic screwdowns eliminate this. There is no backlash with hydraulic screwdowns. Cylinders can be almost any size necessary to create separating forces for the rolling mill. At the hydraulic cylinder are servo valves. The invention of a servo valve was to quickly operate a torpedo toward the direction of the ship. Hydraulic servo valves can allow a drop of oil to move the screwdowns, or if necessary, put in large quantities of oil to position the screwdowns quickly. The screwdowns can be operated with the automatic gauge control system.
Hydraulic screwdowns are powered with a hydraulic pump and tank unit. The pump is usually a pressure compensated pump. The pressure is held at all times into an accumulator so that the hydraulic pressure is ready to go to put one drop or a large quantity of oil into the hydraulic cylinders. The hydraulic cylinders have an encoder to measure with each movement of the hydraulic cylinder, usually .0001”. Some encoders are inside the hydraulic cylinder and some are located outside of the hydraulic cylinder. The encoder tells the position of the cylinder or the roll gap. The usual pressure is a maximum 4,500 PSI.
Usually precision screwdowns work best at higher pressures between 3,000 and 5,000 PSI. New servo valve technology is being developed to operate at up to 10,000 PSI. Movement in the cylinder is done within milliseconds so that the strip coming out of the rolling mill has uniform