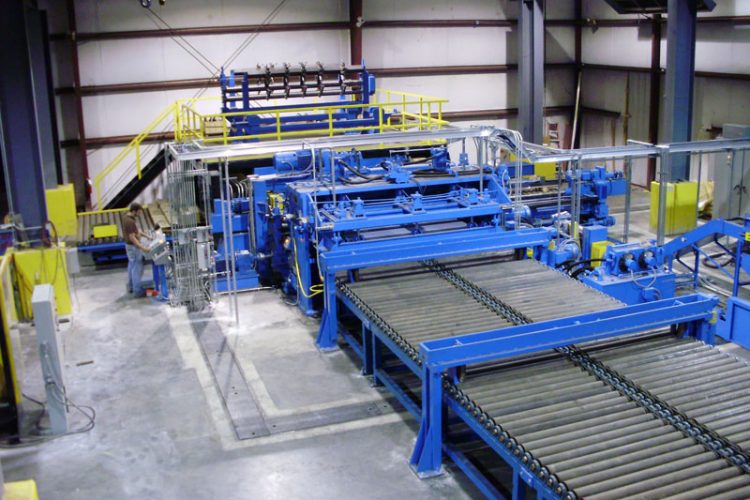
Automatic Gauge Control (AGC) and Direct Gap Control (DGC)
In older rolling mills, a flying micrometer was used for gauge control. A flying micrometer is rollers in a C-frame. The rollers operate an encoder, which tells the position of the gap between two rollers. The micrometer is held perpendicular to the surface of the moving strip. This is called a mechanical gauge. Advancements have been made in this gauge. Instead of using rollers with bearings, it can be a diamond assembly with very little air pressure to measure the thickness. The diamond assemblies are equipped with encoders and located on both sides of the strip so that if you have strip vibration, you are still measuring the thickness of the strip. These mechanical gauges are always on a C-frame and can be removed on a slide during threading. The strip can be inserted into the rolling mill and positioned. The diamond does not require considerable maintenance as it is under very little pressure.
Mechanical gauges are not good for polished material because they can leave a slight line on the surface. An advantage of a mechanical C-frame gauge is the fact that you don’t need to make any adjustments if you are running brass, copper, stainless steel, or steel. If you use a radiation gauge or an x-ray gauge, they may need to be recalibrated for each type of material. In fact, radiation gauge measurement can change from one carbon steel to another. Mechanical measuring of a moving strip has many advantages. It also eliminates the fear of the operator of being around x-ray gauges.
Direct gap control actually measures the distance between the roll gap. Even though the rolls are perfectly concentric, the large back up bearings can be slightly eccentric, and the roll can runout over .001”. With every revolution, there can be a change in thickness of .001” therefore, direct gap control is necessary. If the bearing or roll is not concentric, say .001”, the automatic screw downs with direct gap control can make this correction. Eccentricity may not be from roll grind, but from the bearings themselves. Direct gap control can hold tolerances to ± .0005” with a very simple gauge system.
Mechanical or non-contact radiation gauges, such as gamma or x-ray gauges, are usually located on the entrance and exit sides of the rolling mill. When the strip needs a change in input thickness, it automatically, in microseconds, depending on line speed, adjusts the rolling mill so that a uniform thickness is on the output side. The output side sometimes checks with the direct gap control gauge to assure thickness. At all times, the non-contact gauges are perpendicular to the strip.
To start measuring before rolling is referred to as anticipatory automatic gauge control. When speeds are moving at over 1,000 FPM, adjustments are made in microseconds. In all cases, all of these gauges can be used to operate the hydraulic screw downs. Again, the benefit of hydraulic screw downs is that the cylinder can move upward or downward in microseconds.
The latest non-contact gauges have been developed by American Steel Products using laser technology. They can measure moving aluminum or steel strip at any speed without contact. This new proprietary development is in used today.