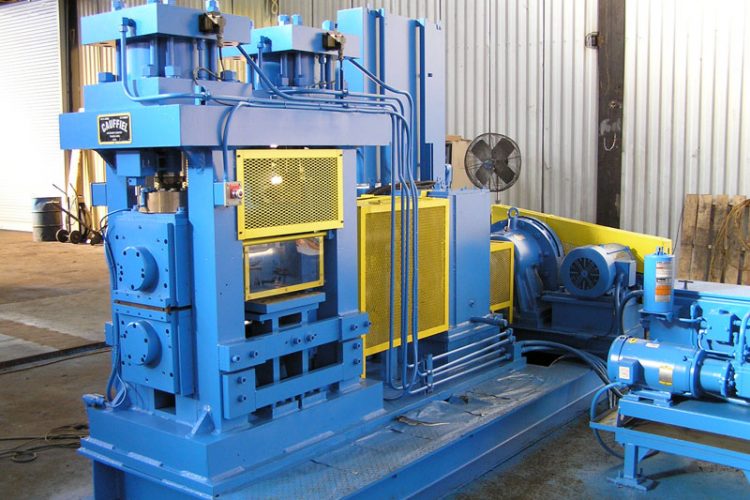
Automation for Reverse Mill Rolling
A pit type coil car receives coils from the rack over a pit. The coil car places the coil onto the single-end hydraulic expanding mandrel uncoiler. The uncoiler is equipped with an electric motor regenerative brake or a water cooled brake system. The uncoiler has a hold down roll and peeler blade that is adjustable up/down and in/out to thread the coil to the flattener pinch rolls.
The flattener with pinch rolls flattens the material. Only the top rolls in the flattener are driven, and the lower rolls spin freely. The material is fed through the pinch rolls of the flattener, across the breaker roll, across the shape roll, through the crop shear, and across an apron through the work rolls. As soon as the material is through the work rolls, the work rolls can come down to take a small reduction.
The material passes through the rolling mill, across an exit apron, through the exit crop shear, shape roll, breaker roll, and is positioned downward onto the drum.
A belt wrapper is used to quickly thread the material around the drum of the recoiler. Once it is threaded on recoiler drum, the outboard hydraulic support can be positioned to assure that the recoiler tension reel does not deflect regardless of tension or coil weight. After a few wraps around the drum, the belt wrapper backs away from the recoiler tension reel, and the mill is now ready to uncoil the coil through the rolling mill onto the other recoiler tension reel at the first pass. Once the tail of the coil is almost through the end of the rolling mill, the material can be put in reverse to the other recoiler tension reel with outboard support. A deep reduction can now be made, one tension reel acting as an uncoiler and one acting as a recoiler. The material goes back and forth two to five times depending upon the amount of reduction with each pass. The coil can be removed from either tension reel by way of the pit type coil car.
As you can see, an operator needs to be equipped with considerable high technology electronics and data recorder for each coil number, each pass, including time for threading, separating force, reduction of each pass, line speed, incoming and outgoing strip tension, and any comments. Also, maintenance schedule and unusual problems with material such as surface finish, coil removal, and reason for downtime should be included.
Modern rolling mills have many hydraulic cylinders, small AC gear motors, modern solenoid valves, flow control valves, heavy pipe, compressed fittings to prevent hydraulic oil from mixing with coolant, and many hydraulic pump and tank units with heat exchangers to assure consistent temperature to assure a minimum of thermal expansion which can cause leaks. All functions can be observed at the control console.