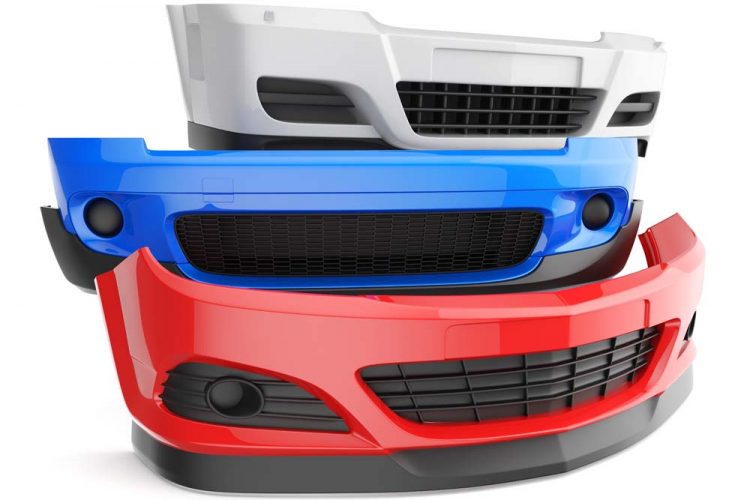
Low Carbon Steels
There are many types of steel that vary in their carbon content. SAE 1006 to 1010 are low carbon steels that are extremely soft and ductile. See table;
Low carbon steels are used for deep draw stampings where the material must elongate, such as when making an automobile fender. These are sometimes referred to as Deep Draw Quality (DDQ). This type of steel starts off with a very low yield strength of 30,000 PSI. As soon as it is cold reduced, and depending upon the amount of reduction, the yield strength can go as high as 100,000 PSI as the material under the work roll hardens. However, as further reduction increases the yield and tensile become about the same and the material will become extremely hard or brittle. This material has now reached its ultimate tensile strength and if bend upon itself, the material will perhaps break, even though the low carbon steel started out very soft prior to reducing. As a rule of thumb, the more carbon content in the steel, that harder it is prior to any cold reduction in a rolling mill.
Some low carbon steel is galvanized (coated with zinc). There are various types of galvanized steel that all have various amounts or weights of galvanized coatings that protect the base metal from corrosion. The thickness of the zinc can be applied very accurately at the coil coater so overall thickness of the coated steel has not increased in gauge very much. Coating weights are measured in grams per meter, one side or both side of the steel coil. So a specified coating weight of 60G/60G would represent a coating weight on both sides of 60 grams per square meter. This type of coating is predominately found in a garbage can or a metal bucket or pail found at the hardware store. Low carbon, galvanized material of the highest possible quality is produced for making products such as automobile panels.
Light gauge (.017”) steel studs and steel framing are also made from low carbon steel. These products are commonly found in walls of commercial buildings and have now found their way into home production as a way to reduce the amount of wooden members previously used over the years. The absence of wood in a home reduces the likelihood of bug infestation and increases the speed of erection as the steel stud and framing member is much lighter that of wood. An industry was developed around the light gauge steel stud because steel mills were unable to produce high quality galvanized steel from .020” to .035” thick on a consistent basis off their rolling mills. As a result, much of this low carbon galvanized steel was sold on the secondary market for products such as steel studs, corrugated steel containers, and mailboxes. Cauffiel built the first rolling mill for reducing secondary galvanized steel from .032” to .017” thick on a high production, continuous basis so that it could be roll formed into a C-section or stud to replace wooden two-by-fours, which ultimately revolutionized the construction industry as we now know it. By reducing material from .032” thick and then down to .017” thick, the material became very strong through work hardening (80,000 to 100,000 PSI yield strength). This makes an excellent stud material for non-load bearing walls due to its stiffness. In fact, the use of steel studs in most commercial buildings became law in many states due to hurricane and NFPA fire codes.